
What to Expect When Budgeting for a Robotic Welding System
The evolution of the industrial landscape continues to see automation scaled from the assembly line to the shop floor. Once a technology imagined and used for Fortune 500 companies with big assembly lines, robotic automation is now a necessity for most small, medium and large businesses alike to keep competitive. Simple to justify for the processing of redundant parts in large-quantity runs for automotive and consumer products in the past, today’s cost-effective robots and automation systems with user-friendly features are tackling tough jobs for a wide range of applications – big and small – in nearly every industry.
The Four D’s
Widely known, as the “4 D’s of Robotic Automation,” there are four types of tasks where robots excel:- Dull jobs are boring and tedious that lead to labor burnout, such as assembly work, repetitive welding or cleaning.
- Dirty jobs present a less than ideal work environment that will also lead to high turnover, like meat processing, warehousing and painting.
- Dangerous jobs put life and limb at risk. This is especially true for foundry, press tending and most welding applications.
- Dear jobs are part of a newer automation “D” family and include tasks that require a specialized or high precision process that is very difficult for a human worker to reproduce. Select aerospace and inspection applications are good examples.
Finding Your WHY to Automate
Once you identify areas that can benefit from robots, there are many intrinsic aspects that help justify what should be automated, and why it makes sense. These “why” objectives should be prioritized and commonly stem from the following reasons: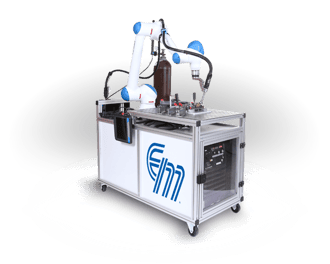
- Increase quality
- Reduce waste and scrap
- Increase throughput
- Reduce labor turnover
- Mitigate skills shortage
- Reduce costs
- Increase health and safety
- Attract new business
- Increase manufacturing flexibility
- Improve supply chain
For most manufacturers, less than two years is expected and perfectly achievable. In some fabrication situations, customers have seen payback even in their first month for high deposition parts and reduced scrap, but in other situations with high-mix parts, payback time may be pushed out to several years.
Electro-Matic’s Mobile Robotic Weld Cart
Electro-Matic’s Mobile Robotic Weld Cart features an adaptive arc with less spatter and improved gap handling, providing increased travel speeds and high-quality welds on a variety of base materials. Simple integration with fixed and flexible automation systems.
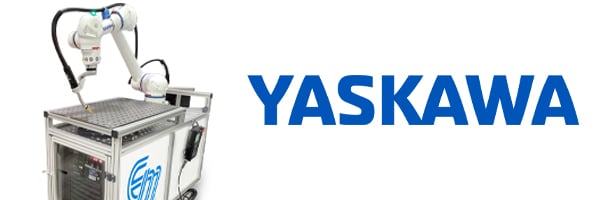